- Large materials are initially crushed by a jaw crusher to the required particle size and then transported by a bucket elevator to the storage hopper.
- From there, they are uniformly and continuously fed into the main unit for grinding by a vibrating feeder.
- The ground powder is carried by the airflow generated by the blower to the classifier for classification. Particles that meet the desired fineness enter the cyclone collector through the pipeline, where they are separated and collected.
- Finally, they are discharged through the discharge valve as finished products. The airflow system operates as a sealed circulation under both positive and negative air pressure.

Brief Introduction
High Pressure Suspension Grinding Mill efficiently handles various non-flammable and non-explosive minerals with hardness up to 9.3 and low moisture. It offers precise control over powder fineness from 50 to 325 meshes (313-45 microns), making it essential for industries requiring precise grinding solutions.
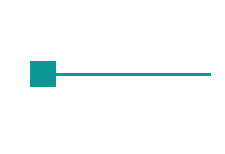
Scope
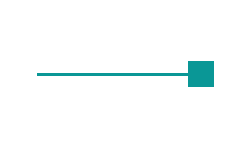
High Pressure Suspension Grinding Mill is used in industries like metallurgy, construction, and mining, grinding materials including quartz, limestone, and more.
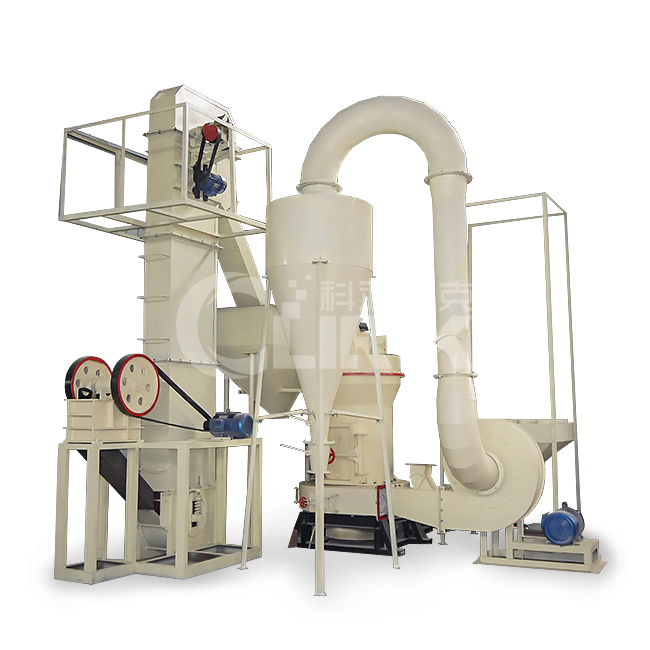
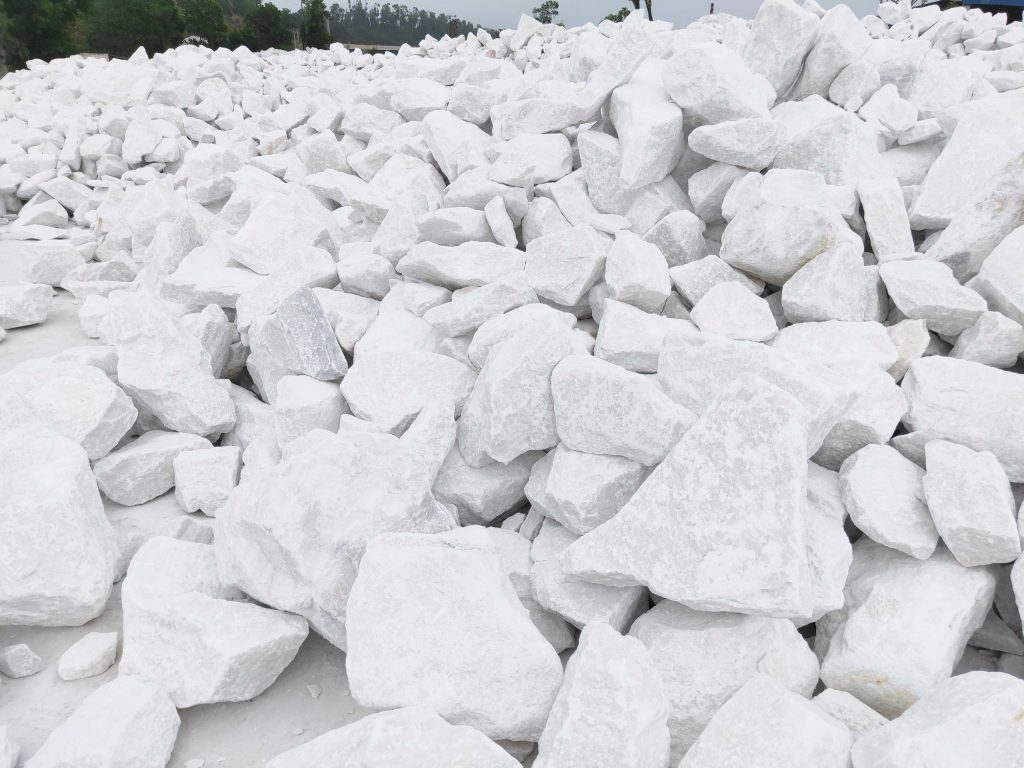
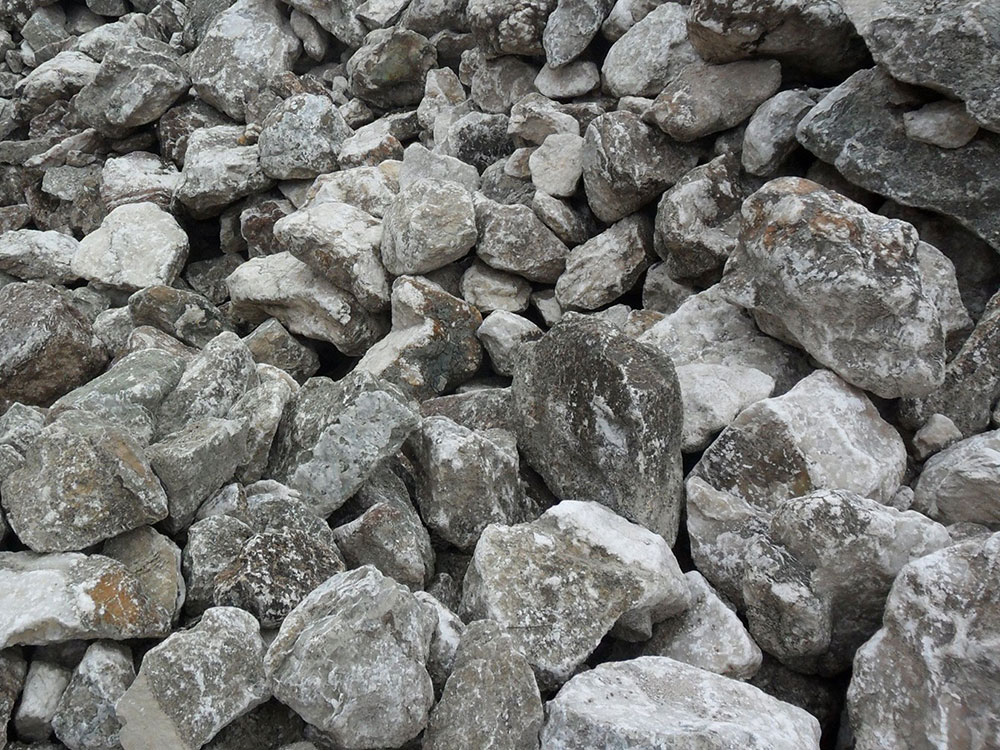
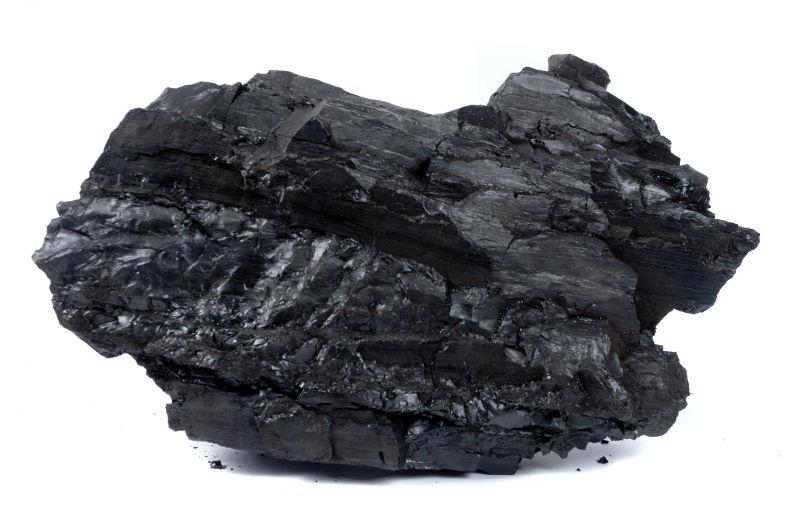
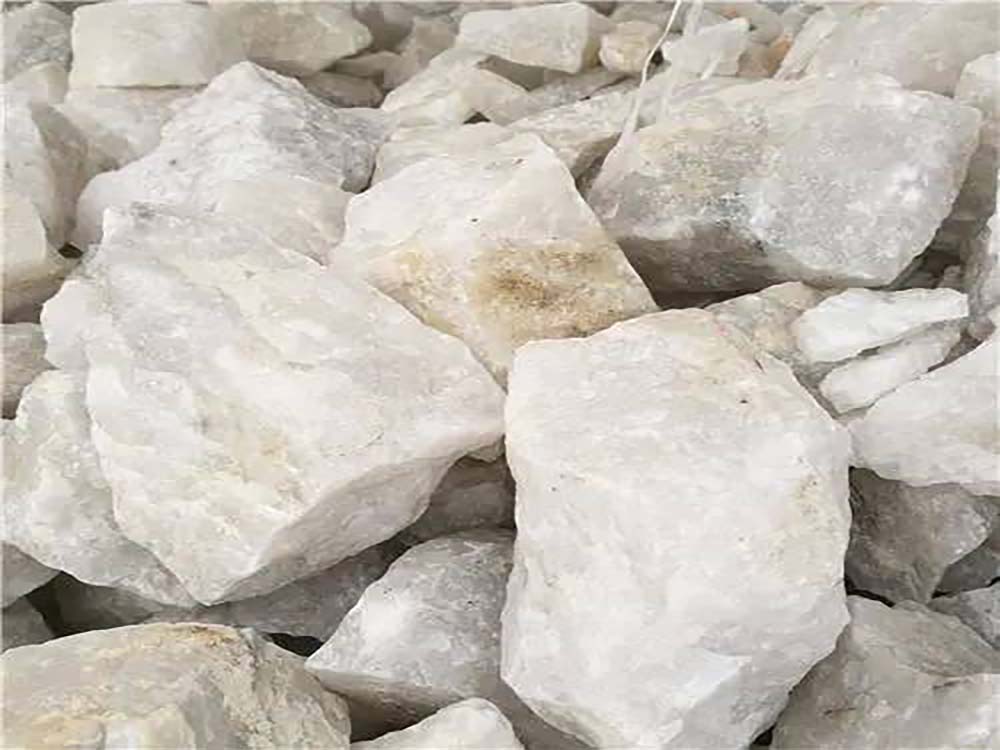
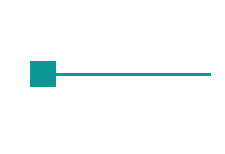
Working Principle
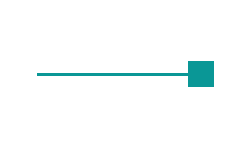
1. Initial Crushing
2. Feeding to Mill
3. Powder Classification
4. Final Collection and Discharge

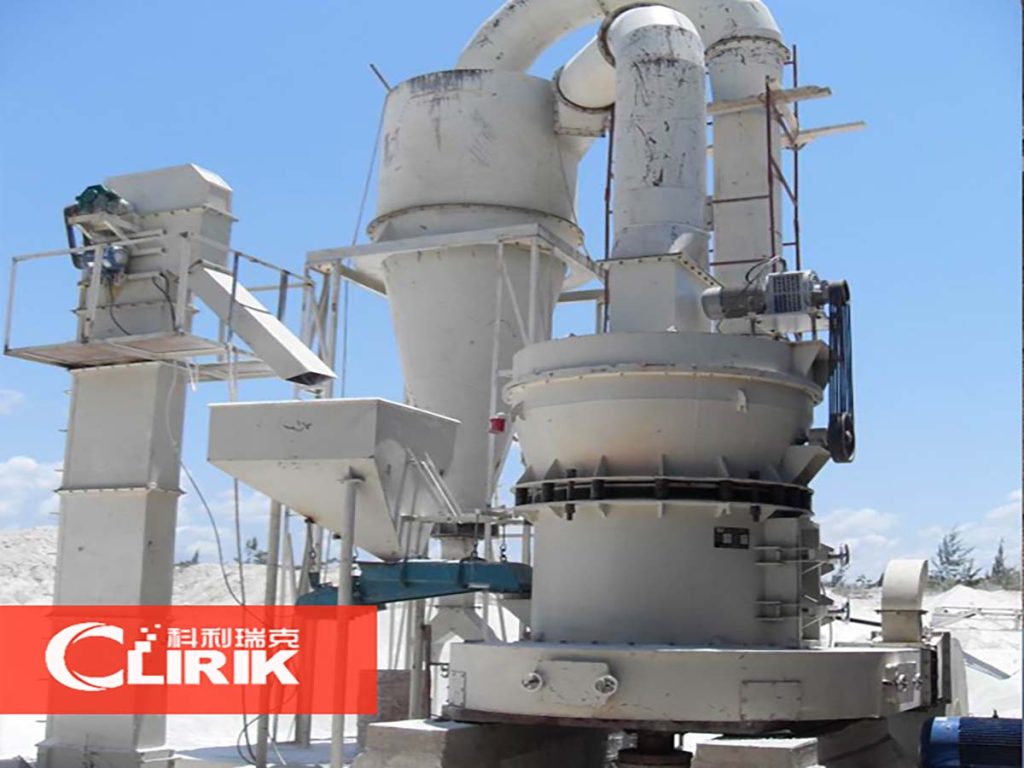
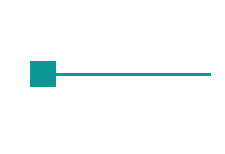
Working Features
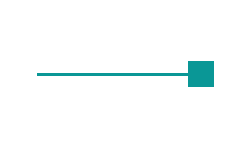
1. High Pressure Spring Design
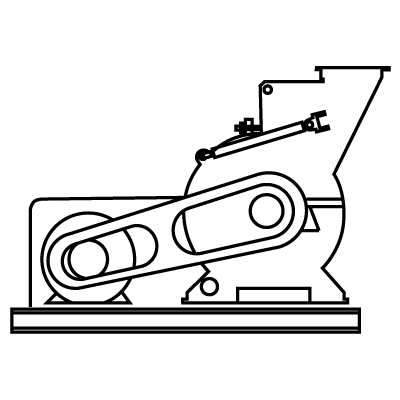
Boosts grinding efficiency with 20-30% increased capacity compared to Raymond mills under similar conditions.
2. Smooth Vibration Reduction Design
Minimizes noise and prevents machine vibrations effectively.
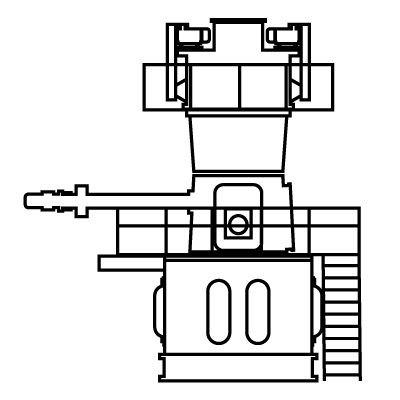
3. Convenient Vane Adjustment Design
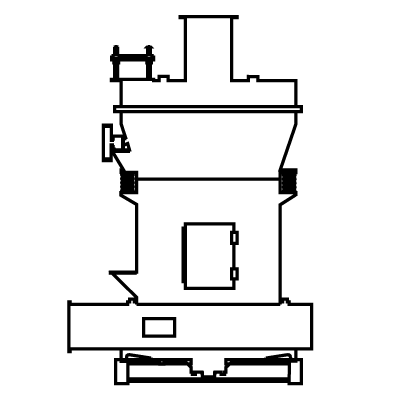
Patented feature allowing easy adjustment for precise control over product fineness.
4. Strong Material Applicability
Suited for materials with Moh’s hardness less than 6, demonstrating versatility.
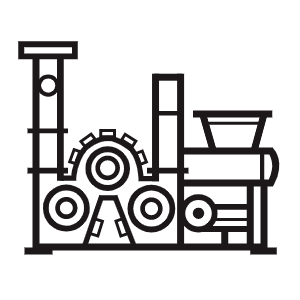
5. Superimposed Multistage Seal
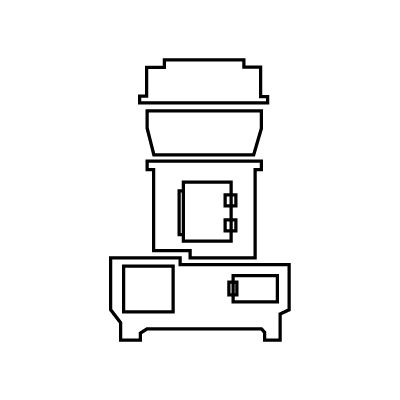
Ensures excellent sealing performance for enhanced operational efficiency.
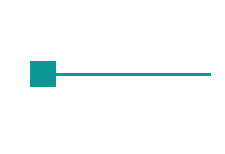
Main Specification
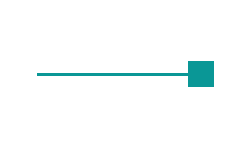
Model | Roller Quantity(piece) | Roller Diameter(mm) | Roller Height(mm) | Ring Inner Diameter(mm) | Ring Height(mm) | Feeding Size(mm) | Finished Size(mm) | Motor Power(KW) | Capacity(t/h) | Overall Dimension(mm) |
YGM7815 | 3 | 260 | 150 | 780 | 150 | 15 | 0.613-0.033 | 18.5 | 1-3 | 4300*3500*5100 |
YGM8314 | 3 | 270 | 140 | 830 | 140 | 20 | 0.613-0.033 | 22 | 1.2-4.6 | 5300*4100*5200 |
YGM9517 | 4 | 310 | 170 | 950 | 170 | 25 | 0.613-0.033 | 37 | 2.1-5.6 | 7100*5900*7900 |
YGM4121 | 5 | 410 | 210 | 1280 | 210 | 30 | 0.613-0.033 | 75 | 2.8-10.5 | 9200*7250*9700 |
YGM1600 | 6 | 440 | 270 | 1600 | 270 | 35 | 0.613-0.033 | 132 | 5-15 | 12550*5700*8350 |
YGM1750 | 5 | 520 | 280 | 1750 | 280 | 40 | 0.613-0.033 | 160 | 7-25 | 11450*7610*9906 |
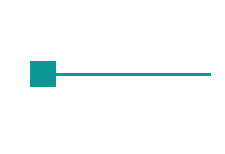
Other Main Products
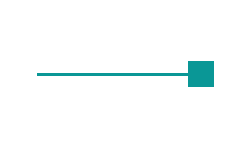
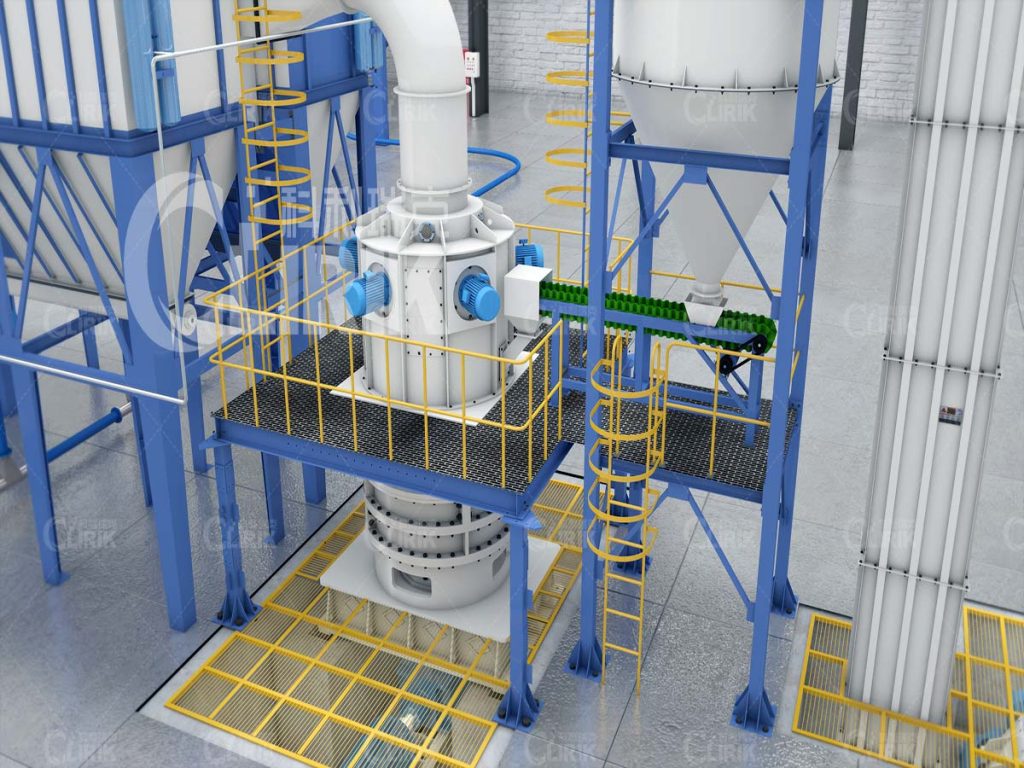
Clirik’s HGM Micro Powder Mill is known for stability and low maintenance, ideal for fine milling of over 100 brittle materials like calcite and limestone.
Clirik’s European Coarse Powder Mill is used in industries like metallurgy and construction, crushing rocks up to 320 MPa into coarse powder, with most particles under 3mm.
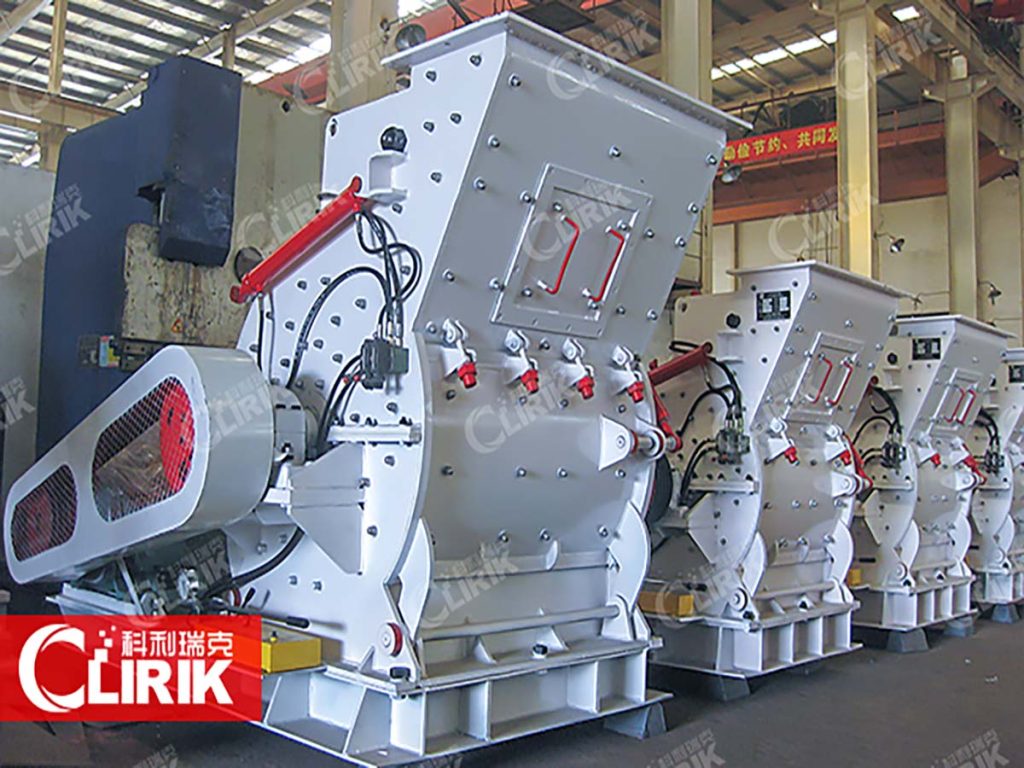
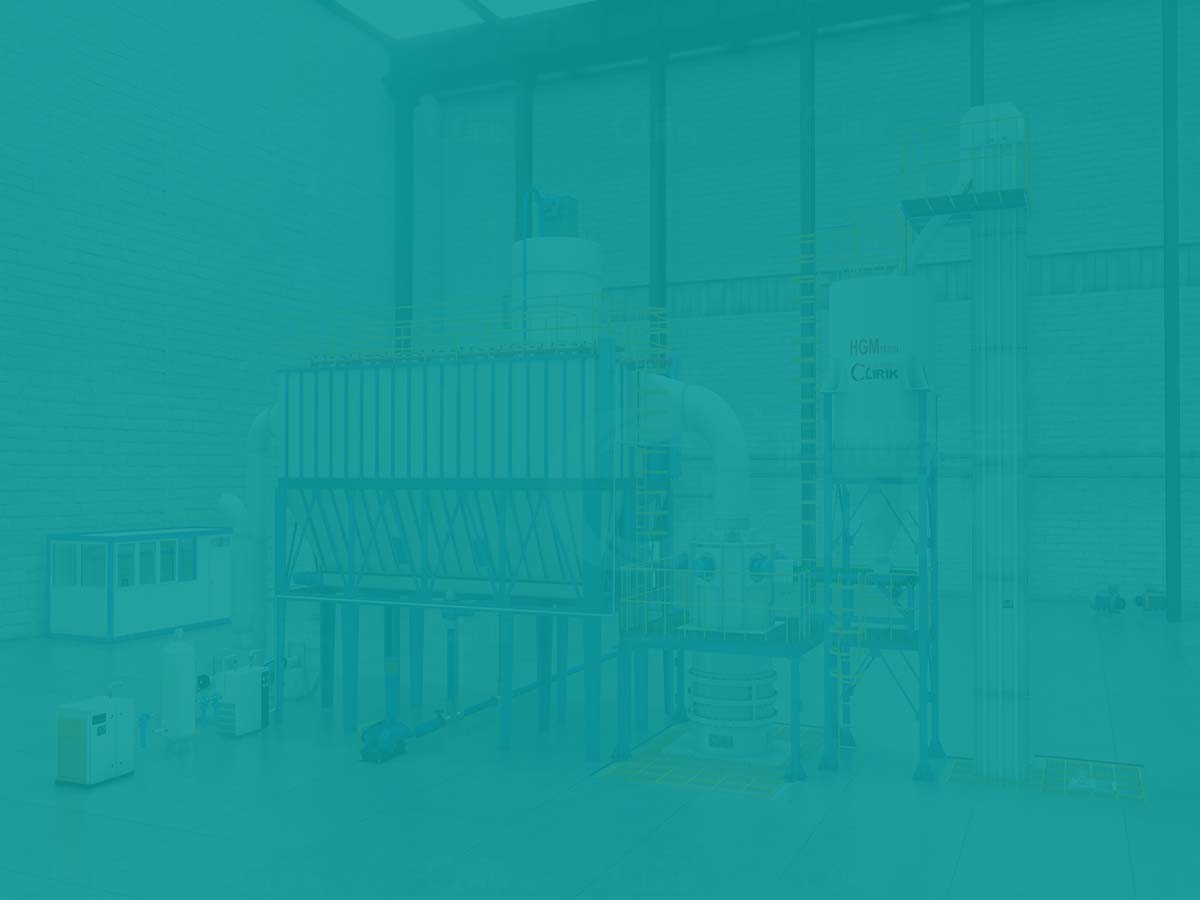
Shanghai CLIRIK Machinery Co.,Ltd. has dedicated itself to the ultrafine powder grinding machine industry for two decades.
Welcome to visit our factory in No.19 Fuqing Rd, Pudong New Area, Shanghai201201, China.
You can leave a message online or contact CLIRIK directly:
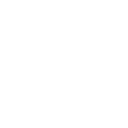
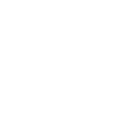